
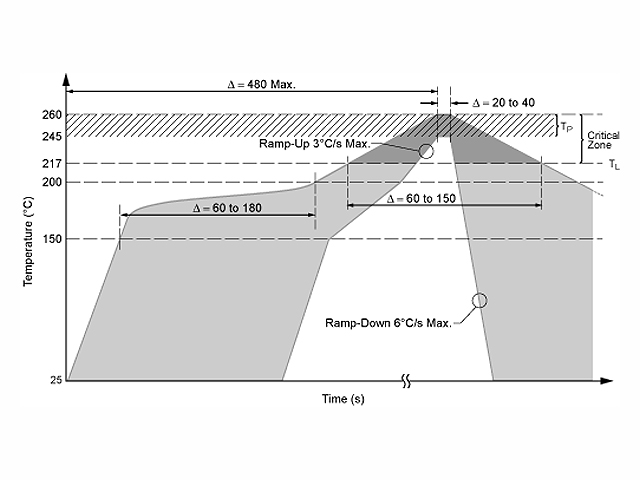
How long an oven do I need to process boards at this throughput? The solder paste manufacturer recommends a 4 minute, three step profile. Process speed = Oven chamber heated lengthīelow is an example of calculation to establish the correct oven size:-Īn SMT assembler wants to produce 8-inch boards at a rate of 180 per hour.
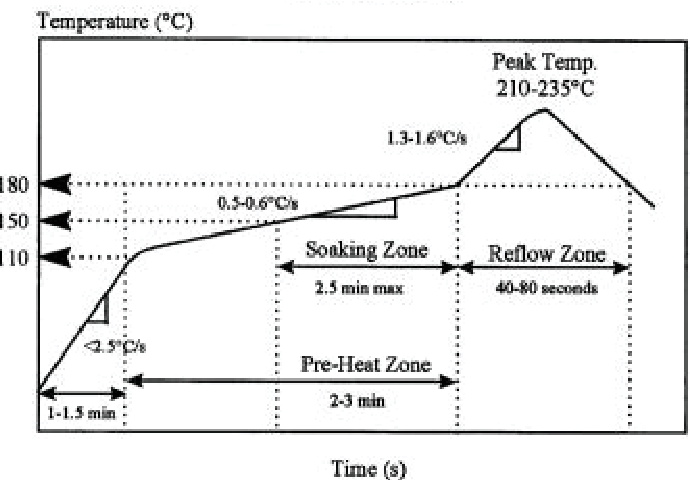
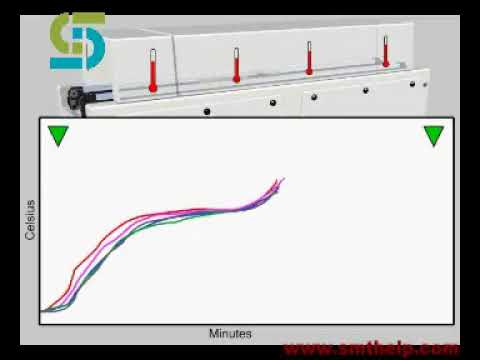
The temperature of 180 is kept constant (Soak zone) before it is increased again to reach its spike value.Īs Observed for Lead-free solder, the temperature keeps rising gradually to reach its maximum (spike) value.To be able to select the correct size reflow oven the process speed (defined below) must be greater than the minimum calculated line speed. Ramp Soak Spikes are primarily used for Leaded Solder and Ramp-to Spike profiles are suggested for Lead-Free solder.Īs mentioned in the table above, for Leaded solder the preheat stage usually starts at 150 and is increased to 180. Ramp soak spike profile indicates the temperature that is subjected to a given PCB is allowed to rest in the Soak zone (constant temperature value) before the temperature is increased again to hit the spike (maximum value).įor the Ramp to Spike Time-Temperature profile, the temperature is increased gradually without to reach its maximum value (Spike). So it is important to evaluate the reflow profile of the solder being used. Reflow Zone: The reflow zone allows the temperature to rise again (by 3 every 1 second) till it reaches the spike value so that the applied solder begins to melt and start wetting with the copper surface which helps in creating better solder joints.Ĭooling Zone: The cooling zone is the profile where no additional heat is applied to the PCB and air is supplied to supplement the cooling process such that the temperature is decreased at a rate of 4 at every 2 seconds so that the freshly created solder joint is solidified.ĭifferent types of solder have different reflow profiles. Soak Zone: In the Soak zone, the temperature achieved through preheat zone is maintained so that the FLUX applied on the board is activated and constant temperatures can be maintained for all components present on the board. Hence to prevent this, the PCB is subjected to preheating where the temperature is increased by 3 every 1 second. It cannot be subjected to high heat suddenly as there is the risk of thermal shock which can cause the components on the board to explode, melt or become nonfunctional. Preheat Zone: Initially the PCB is at room temperature. The reflow profiles are divided into four zones: Reflow profiling is used to optimize the soldering process by minimizing the drastic change in temperatures which might cause cold solder joints, charred boards, tombstoning and uneven wetting. In the reflow soldering process, the board with solder should be heated in a way to ensure that the solder melts and solidifies at particular temperatures over specific periods of time to ensure proper solder joints are formed. Reflow profiling is the process of evaluating the effect of heat on the solder being used on a printed circuit board.
